Proper concrete mixing is as important as the concrete quality and its constitution. To assure good quality and strength all the ingredients of the mix should be combined thoroughly. Proper mixing process should be carried out as it will get us a homogeneous mass of uniform concrete. Uniform mixing of the concrete gives you good consistency and color thus producing the desired concrete that is workable and facilitates compaction. Gone are those days when concrete was mixed manually. Today all the mixing is done by the concrete mixing machines. Whether the concrete plant is a small scale or large scale these machines have taken over all the areas, providing good consistency and efficient mixture. They also reduce the time consumption.
With more and more infrastructural development coming up the concrete industry is growing fast. Thus different types of mixing machines have come into the market. For small scale and large scale sectors there is a wide range concrete mixing machines that can fit into the type of concrete mixing plant you have the project on. Whatever the sector is, continuous mixing process should be given importance. The mixing should run throughout the concreting period until desired concreting is achieved. Hence we can say that that concreting is a non-stop process in the industry. To achieve this, it is very important to maintain the concrete mixer.
Before the operations are commenced it is very important that the operator have read the maintenance and working manual. The maintenance process can be carried out in a daily, weekly and monthly manner. But apart from timely checking there are some common points to be taken care of.
- The mixer should be at a leveled platform in the construction site and should also be firm enough to hold the machine.
- After the mixing operation the blades of the device should be cleaned properly.
- The skip must be supported properly with a sand bag cushion and should be operated carefully.
- When it is not in use the drum should be in a tilted position or covered, so as to avoid catching rain water or any other water.
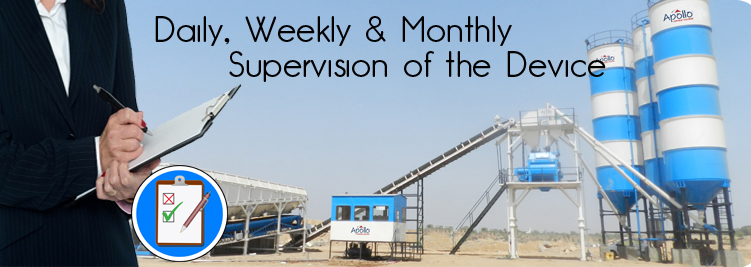
- Before beginning the daily routine, check the machine for any waste concrete or any build up on the wall or floors of the mixer. Remove them if present.
- When the production takes and extended break, apply high pressure wash.
- At the end of the day clean the mixer with a high pressure washer.
- The discharge chute should also be checked clean.
- While cleaning any type of build up in the blades, arms, walls and floors, metal hammers are a big no. use plastic hammers instead as the parts are cast iron and metal hammers can make tem brittle.
- Make sure that the door seal is clear of build up.
- The clearance between the floor of the mixer and mix blades should be checked and adjusted to approx 3mm.
- Check the clearance of the blades to the floor and wall tiles before starting the device and do adjustment accordingly.
- The bolt tightness should be taken care of after every adjustment.
- The oil level in the hydraulic should be revisited every time to assure that there is no leakage.
- The gearbox should be greased at proper time intervals.
- Ignore casting blow holes and walls should be analyzed for any damage.
- The spray heads of the high pressure washer have to be cleaned with a wire brush so as to avoid concrete build up in the nozzle.
- Inspect leakage and replace the door seal if any.
- Using a dipstick to check the oil level, it shouldn’t be overfilled.
- Change the gearbox oils to avoid emulsification and contamination.