Table of Contents
The modern construction and precast concrete industry increasingly rely on advanced automation to improve efficiency, precision and consistency. At the heart of many reinforced concrete applications lies the cage welding machine, a pivotal piece of equipment in producing structural reinforcement cages. These machines have evolved significantly, thanks to engineering innovations focused on improving productivity while reducing operational downtime.
This article explores the cutting-edge technologies that shape today’s cage welding equipment, particularly in the areas of chain-controlled diameter adjustment, closed-circuit water recooling systems and enhanced material handling mechanisms such as holding trays and wire decoilers. Together, these features contribute to superior welding performance and long-term reliability, making them essential components in next-generation automatic cage welding machines.
Testimonials
“India’s Largest Construction Equipment Manufacturing Company since 2008. ”
Precision Through Chain-Controlled Diameter Adjustment
One of the most critical requirements in reinforcement cage fabrication is maintaining dimensional accuracy throughout the production process. Manual adjustments often lead to inconsistencies and delays. To overcome this, modern cage assembly machines now integrate chain-controlled diameter adjustment systems that offer unmatched precision and flexibility.
Advantages of Chain-Controlled Diameter Systems:
- Rapid adaptability: Operators can adjust cage diameters swiftly without halting production. This makes it easier to accommodate a variety of project specifications with minimal downtime.
- High accuracy: The mechanical precision of the chain system ensures that diameter tolerances remain extremely tight, which is vital for structural integrity in large-scale applications.
- Automation-friendly: Chain systems integrate seamlessly with programmable control units, allowing preset diameters to be selected through simple interface inputs.
This advancement not only reduces the dependency on operator skill but also allows manufacturers to produce precise and straight cages compatible with all major construction standards. It ultimately enhances the operational capability of reinforcement cage welding machines, particularly in high-volume production environments.
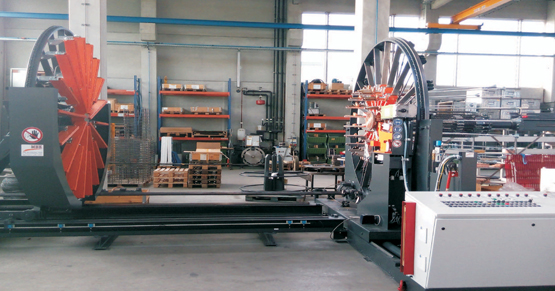
Enhancing Equipment Longevity with Closed-Circuit Water Recooling
Welding generates a substantial amount of heat, which can degrade equipment performance if not managed properly. Traditional cooling systems often rely on open-loop water circulation, leading to excessive water consumption, scaling and maintenance issues. In contrast, modern cage welders now employ closed-circuit water recooling systems that offer a host of performance and sustainability benefits.
Key Features and Benefits:
- Minimal maintenance: Closed-circuit designs only require an initial water fill, drastically reducing the need for constant monitoring and refills.
- Consistent cooling efficiency: The system maintains optimal temperature levels throughout prolonged operation, preventing thermal overload and extending equipment life.
- Protection against corrosion and scale: As the same water circulates in a sealed loop, impurities and contaminants are minimized, keeping internal components clean.
- Compact and integrated: These systems are often built into the welding machine itself, saving space and simplifying plant layout.
Operators of automatic cage welding machines benefit greatly from these systems, particularly when operating in regions where water conservation is crucial or where downtime caused by overheating can be costly. It’s a clear example of how innovation in peripheral systems can boost the overall efficiency of a welding machine.
Improving Workflow with Holding Trays and Wire Decoilers
Efficiency in cage production doesn’t depend solely on the welding process – it also requires effective material handling. Feeding reinforcement wire and maintaining an uninterrupted workflow are critical. That’s where smart innovations like holding trays for longitudinal bars and winding wire decoilers come into play.
Holding Trays for Longitudinal Reinforcement:
- Heavy-duty capacity: With the ability to handle up to 1 ton of material, these trays significantly reduce the frequency of material reloads.
- Improved alignment: Trays help maintain consistent feed alignment, which is essential for automated welding systems.
- Time-saving: Operators spend less time handling materials, allowing more time for monitoring production and quality control.
Wire Decoilers Without Cut-Off Ramps:
- Fixed and stable design: Unlike traditional ramped decoilers, the fixed version ensures smoother wire feeding, minimizing tangles and material waste.
- Simple guidance system: The wire guide leads directly to the welding roller, reducing friction and preventing feeding errors.
- Compact structure: These systems take up less floor space and simplify overall machine integration.
Both these components improve the overall efficiency and reliability of cage welding equipment, making them indispensable for large-scale operations. They support continuous production and reduce the likelihood of human error, contributing to higher throughput and better product quality.
Integrated Safety and Structural Enhancements
While performance and efficiency are essential, safety remains a foundational aspect of any welding operation. That’s why modern cage welder systems come equipped with robust safety enhancements, including:
- Light barriers: Positioned separately for the feeding and cage removal sides, these prevent accidental entry during machine operation.
- Security fencing: Installed on both sides and the central division area, these fences protect operators from mechanical hazards while maintaining visibility and access control.
- Emergency stops and locking systems: These ensure that machinery can be halted instantly in case of any unsafe condition or operational anomaly.
Such safety features not only protect personnel but also reinforce machine durability by preventing accidents that might lead to costly repairs or replacements.
Performance Synergy: How Innovations Work Together?
Each of the innovations discussed – diameter control, water cooling, material handling – functions individually to improve cage welding machine operations. However, when combined, their impact multiplies, leading to:
- Higher production rates
- Consistent weld quality
- Lower operating costs
- Extended machine life
- Reduced human error and intervention
These improvements make modern automatic cage welding machines highly attractive to both large-scale precast facilities and smaller workshops looking to enhance their efficiency without compromising quality.
Client Speaks
“Good quality equipment product company.”
Conclusion
The evolution of cage welding equipment reflects the broader industrial shift toward precision, automation and operational efficiency. Innovations in diameter adjustment systems, closed-circuit water recooling and smart material handling not only enhance machine performance but also reduce overhead costs, improve safety and streamline production.
For anyone in the reinforcement cage production field – be it engineers, plant operators or procurement managers – understanding and investing in the latest cage assembly machine technologies may provide a significant competitive edge. As the demand for high-precision construction components rises, so too will the value of machines that deliver reliability, flexibility and efficiency in every weld.
Table of Contents