Introduction
There has been an increase in the utilization of automated machines that manufacture high quality and uniformly mixed products. To obtain maximum efficiency during construction, central mix or batching devices need to be used.
This equipment adequately mixes ballast, cement, sand, and other additives to produce a homogenous mix that raises the durability, strength, surface finish, fire resistance and other properties of buildings.
Economic analysis of the machines
Onsite devices allow easy and fast mixing of the aggregate which result to drastic cost reduction. The price of producing one ton of concrete is much lower when using this equipment as compared to the other mixers or manual mixing.
These plants are only economical when installed at the site or near the building area. When they are too far, the transportation charges are very high.
Trends in India and other parts of the world
With the rapid increase in large construction sites in India, the demand for compact batching plants use will rise. Small residential building projects did not use this equipment but with rapid development of modular and small machines, their use is becoming common.
With a very high population of 1.25 billion, good GDP per capita ($4,247) and ease of getting credit and high global competitiveness, India construction business is set to rise. According to 2013 estimates, the industry was valued as $126 billion and total spending of $ 427 billion.
According to PWC, the global building volume is set to increase to $ 15 trillion by 2025. Most of these constructions will be on emerging markets such as China and India. By 2025, China, India and US will account for 60% of all construction. By 2010, China was leading in this market. It is expected that construction quality and regulations will necessitate the use of the machines.
Case studies on the use in real estate
This equipment has been successfully used in local and international real estate projects. Though not widely used in real estate market due to transportation charge limitations, it is expected that this trend will increase in the future.
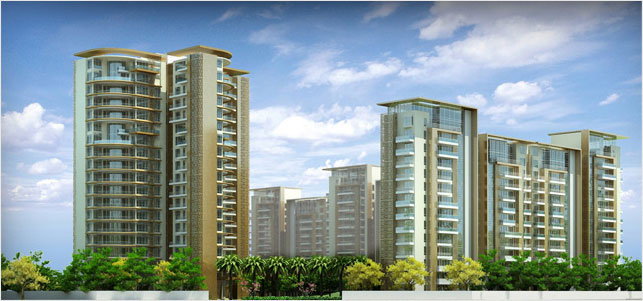
Case studies on the use in industrial and infrastructure projects
Industrial constructions sites are large and require contracted works. Most of these sites utilize batch machines to increase productivity. The current cost of production is Rs.7 to Rs 8, for every 100 m3. The use of ready mix ballast which started in Mumbai is slowly and successfully being applied in other large cities and metropolitan areas.
Critical quality and productivity benefits associated with batching plant
The average hourly output for these equipment is far much higher that other mixers. Typical plants produce 25-200m3/hr depending on the size. Smaller semi batchers generate 8-30 M3/ hr. When using manual labor, these volumes will require many laborers and supervisors.
Small mobile systems that can be easily dismantled folded and installed at large building sites save transportation and labor cost. They save between 500-1000 Rs per 1000m3. In addition, projects can be finished within schedule and cost.