Table of Contents
A well-designed concrete batching plant makes all the difference in construction efficiency. Proper layout, equipment selection and automation ensure consistent concrete quality, lower maintenance and faster operations. Poor design leads to delays, material waste and costly breakdowns.
Apolloinffratech offers popular batching plant design based on project needs. Choosing the right design impacts output, cost-effectiveness and site adaptability.
This article explores why concrete batching plant design is critical and how the right setup improves performance.
Why Design Matters in Concrete Batching Plants?
1. Concrete Batching Plant Increases Production Efficiency
A good concrete batching mixing plant design optimizes material flow, reducing waiting time. Inline plants, for instance, allow continuous mixing, while compact models improve mobility for smaller sites.
2. Batching Plants Reduces Material Waste
Properly planned batching plants prevent material spillage and ensure accurate weighing. This reduces waste and improves cost savings.
3. Concrete Batching System Enhances Concrete Quality
Mixing consistency depends on plant design. Efficient concrete batching equipment minimizes variations, ensuring every batch meets project standards.
4. Concrete Batching Machine Lowers Maintenance Costs
Plants with robust structures and easy-to-access components require less maintenance. Choosing a durable concrete batching plant design prevents frequent repairs.
5. Concrete Batching Plants Improves Site Adaptability
Every construction site has different requirements. A well-designed plant, whether inline or compact, can fit site conditions and project scale.
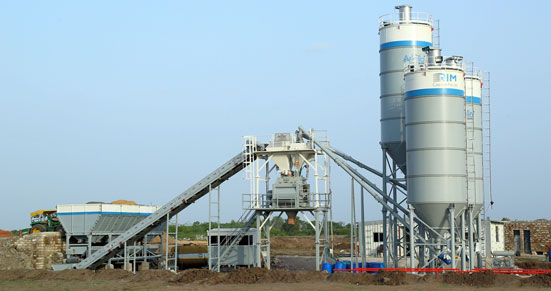
Inline Concrete Batching Plant Design: Precision & Large-Scale Operations
An inline concrete batching plant is ideal for medium to large projects. It features multiple aggregate bins aligned in a row, allowing efficient material handling and continuous production.
Model-Specific Highlights of Inline Batching Plants
- ATP 30: Best for small to medium projects, compact yet powerful.
- ATP 45/60/75: Modular design for medium to large-scale projects.
- ATP 90/100/120: High-output plants for industrial-scale projects.
These concrete batching plant manufacturers provide inline plants that optimize project efficiency and offer cost-effective solutions.
Compact Concrete Batching Plant Design: Space-Saving & Mobility
A compact concrete batching plant is designed for smaller spaces and quick relocation. It requires minimal foundation and setup time, making it ideal for mobile or temporary projects.
Design Features of High-Quality Compact Batching Plants
- Strong Steel Frame: Built from square and rectangular tubes for longevity.
- Dust & Water Protection: Covered motors and quick exhaust valves enhance durability.
- Electrical Safety: MPCB safeguards all electrical components.
- Quick Operation: Faster weighing and mixing cycle for better productivity.
These features ensure that compact concrete batching plants remain cost-effective and reliable for diverse construction needs.
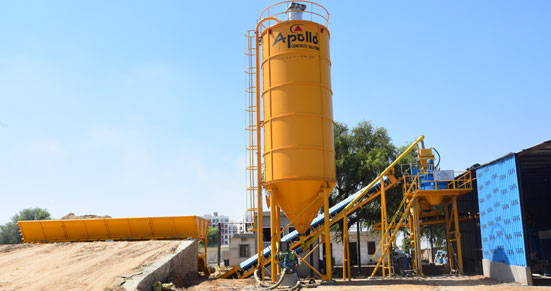
Key Design Considerations for Concrete Batching Plants
1. Type of Project
- Large infrastructure projects need high-capacity inline concrete batching plants.
- Smaller projects benefit from compact concrete batching plants for flexibility.
2. Available Space
- Inline plants require more space but offer higher output.
- Compact models fit tight locations with minimal site preparation.
3. Concrete Mix Requirements
- Complex concrete formulations need advanced equipment.
- Simple mixes work well with smaller, easy-to-maintain plants.
4. Automation Level
- Fully automated plants improve precision but may cost more.
- Semi-automated plants offer a balance between efficiency and affordability.
5. Mobility Needs
- If relocation is frequent, a compact concrete batching plant is ideal.
- Fixed sites work best with inline batching plant design for higher output.
Future Trends in Concrete Batching Plant Design
1. Energy-Efficient Designs
Manufacturers are improving plant efficiency, reducing power consumption and optimizing material use.
2. Prefabrication Integration
With increasing demand for precast construction, batching plants now support faster prefabricated structure production.
3. Compact & Modular Growth
More builders prefer compact concrete batching plants for their quick installation and easy transportability.
Conclusion
A well-designed concrete batching plant increases efficiency, reduces costs and ensures quality output. Inline concrete batching plants suit high-volume projects with modular expansion capabilities. Compact concrete batching plants are ideal for mobile and space-limited applications.
Choosing the right concrete batching plant design prevents downtime, lowers maintenance costs and ensures smooth operations. Whether you need a high-capacity inline plant or a flexible compact model, investing in the right design is key to project success.
Read More Articles on Concrete Batching Plants
- How to Choose the Best Concrete Batching Plant for Your Needs?
- Maintenance Tips for Keeping Your Concrete Batching Plant in Top Condition
- Latest Trends in Concrete Batching Plant Technology: A 2025 Outlook
- Economic Series Concrete Batching Plants for Infrastructure Projects in Rural India
- How Compact Batching Plants Improve Construction Timelines?
Table of Contents