Table of Contents
The efficiency of any construction project depends on selecting the right concrete batching plant. The capacity of the plant determines the speed and volume of concrete production. A high-capacity plant can handle large infrastructure projects, while a low-capacity plant works well for small-scale and mobile applications.
Choosing between an inline concrete batching plant and a compact concrete batching plant is crucial. Each type offers unique benefits depending on project size, location and budget. This article explains the key differences, technical specifications and best applications for each type.
What is Concrete Batching Plant Capacity in a Batching Plant?
The concrete batching plant capacity is the amount of concrete it produces per hour, measured in cubic meters per hour (m³/h).
- Low-capacity plants: Produce 25 to 75 m³/h of concrete.
- High-capacity plants: Produce 90 to 120 m³/h or more.
Choosing the right capacity depends on the project’s concrete demand, timeline and site conditions.
High-Capacity Concrete Batching Plants: Operational Standards
An inline concrete batching plant is built for large-scale projects such as highways, bridges, airports and industrial buildings. These plants offer continuous and high-output production, ensuring faster project completion.
1. Features of High-Capacity Inline Concrete Batching Plants
Models Available:
- ATP 30 – Best for mid-size projects.
- ATP 45, ATP 60, ATP 75 – Suitable for growing infrastructure needs.
- ATP 90, ATP 100, ATP 120 – Designed for large-scale construction.
Technical Advantages:
Inline Batching Plants Offers Structure & Durability:
- Built with square and rectangular tubes for strength.
- Corrosion-resistant materials ensure longevity.
Batching Plant System:
- Uses a 3-batch system to achieve 90% of theoretical output.
- High-efficiency mixers ensure uniform concrete consistency.
Inline Batching Control System:
- PLC-based automation for precise weighing and batching.
- Eliminates manual errors and increases efficiency.
Weighing & Accuracy with Inline Concrete Batching Plants:
- Quick exhaust valves in pneumatic cylinders maintains accuracy.
- High-precision weighing system prevents material waste.
Electrical & Safety Features:
- Equipped with MPCB (Motor Protection Circuit Breaker) for all motors.
- Protective covers on motors safeguard against dust and water.
Inline Concrete Batching Provides Efficiency & Maintenance:
- Designed for continuous operation in industrial projects.
- Requires minimal maintenance, reducing downtime.
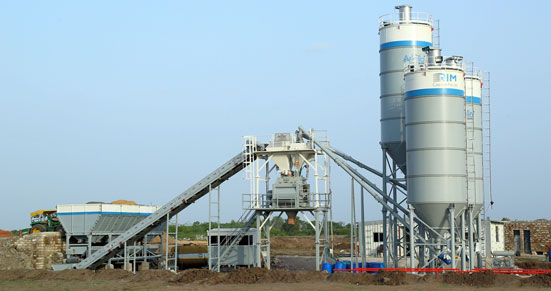
2. When to Choose a High-Capacity Plant?
- For large-scale infrastructure projects.
- When continuous concrete supply is needed.
- If the project demands multiple concrete mix variations.
- When high automation is required for precision.
A high-capacity concrete batching plant ensures speed, consistency and reliability. However, it requires more space and higher investment.
Low-Capacity Concrete Batching Plants: Specifications
A low-capacity concrete batching plant is designed for small-scale projects, mobile applications and sites with space constraints. These are cost-effective and easier to install and operate.
1. Specifications of Compact Concrete Batching Plants
Models Available:
ATP 25, ATP 31, ATP 45, ATP 61, ATP 75 – Suitable for small to mid-scale projects.
Technical Advantages:
Compact Concrete Batching Plant Offers Structure & Durability:
- Robust square and rectangular tubes for strength.
- Corrosion-resistant materials for extended life.
Foundation Requirement of Batching Plant:
- Only PCC Required, making installation quick and cost-effective.
Compact Concrete Plant Provides Space Efficiency:
- Compact design requires minimal space, perfect for urban projects.
Compact Batching Plant Supports Operation:
- Simple to erect, operate and maintain.
- Requires minimal manpower for daily operations.
Weighing & Conveying System:
- Single weighing and conveying belt for faster cycle time and increased output.
- Quick exhaust valve ensures accurate weighing.
Electrical Safety with Compact Concrete Batching Plant:
- MPCB (Motor Protection Circuit Breaker) safeguards motors.
- Dust and water protection for electrical components.
Efficiency Using Compact Batching Plant:
- Low running costs with high output.
- Ideal for small contractors and budget-conscious buyers.
2. When to Choose a Low-Capacity Plant?
- For small-scale construction sites.
- When space for installation is limited.
- For temporary or mobile projects requiring quick setup.
- If budget constraints limit large investments.
A compact concrete batching plant offers flexibility, affordability and efficiency, making it perfect for smaller projects.
Comparing High-Capacity vs. Low-Capacity Batching Plants
Feature | High-Capacity Batching Plant | Low-Capacity Batching Plant |
Best for | Large infrastructure projects | Small to mid-size projects |
Production Capacity | 90 to 120 m³/h | 25 to 75 m³/h |
Space Requirement | Requires large installation area | Compact design, fits small spaces |
Foundation | Needs a strong foundation | Only PCC required |
Installation Time | Longer setup time | Quick installation |
Cost | Higher investment | Cost-effective |
Automation | Fully automated for precision | Simple and easy to operate |
Mobility | Fixed at one location | Can be relocated if needed |
This comparison helps determine which concrete batching system best fits project needs.
Factors to Consider When Choosing a Concrete Batching Plant
1. Project Size & Scope
- Large infrastructure projects need high-capacity concrete batching plants.
- Small-scale projects or mobile applications work better with low-capacity batching plants.
2. Space Availability
- Inline batching plants need more space and proper foundations.
- Compact batching plants fit into tight locations without additional setup.
3. Budget Constraints
- High-capacity models involve greater investment but yield higher output.
- Low-capacity models reduce upfront costs and are more affordable.
4. Concrete Production Requirements
- For high-volume, continuous production, choose an inline concrete batching plant.
- For flexibility and easy transport, go for a compact concrete batching plant.
Conclusion
Selecting the right concrete batching plant depends on project needs, space, budget and production requirements. High-capacity batching plants are best for large-scale infrastructure projects requiring high output and precision. Low-capacity batching plants are ideal for smaller jobs, mobile applications and budget-conscious buyers.
By understanding concrete batching plant capacity, features and project demands, buyers can invest in the right equipment for efficiency and cost savings.
Read More Articles on Concrete Batching Plants
Table of Contents