Table of Contents
In the world of large-scale infrastructure, deadlines are tight, quality is non-negotiable and delays can cost millions. Whether it’s highways, metros, industrial complexes or high-rise buildings, the success of these projects often hinges on the reliability and efficiency of the concrete batching plant on site. That’s where the inline batching plant proves indispensable. Designed to deliver consistent and high-volume concrete supply, inline plants like ATP series are now the preferred choice for infrastructure giants worldwide.
As construction projects become more ambitious in scope and complexity, traditional concrete production methods often fall short. The inline concrete plant fills this gap by combining high output with operational efficiency, reduced maintenance requirements and adaptability to a wide range of concrete mixes. In this guide, we explore how these plants meet the unique challenges of industrial-scale construction, especially with advanced models like the ATP 90, 100 and 120.
Testimonials
“Strongly agree for 5 star rating.”
Significance of Inline Batching Plant System
Unlike other batching configurations, the inline type batching plant features a linear layout of aggregate bins and material feeding systems. This design facilitates a faster, smoother process with minimal manual intervention. The inline setup ensures that aggregates, cement, water and admixtures are systematically weighed and fed directly into the mixer. The result is a continuous and uninterrupted flow of concrete production, ideal for time-sensitive infrastructure developments.
Core Advantages of Inline Batching Systems:
- Better material flow: The sequential layout enhances aggregate flow, reducing segregation and batch inconsistencies.
- Enhanced automation: Most inline systems, particularly from advanced series like ATP, include programmable logic controllers’ interfaces for seamless monitoring.
The integration of these design features into each inline concrete mixer ensures high repeatability, precise dosing and consistent output, even under intense project pressure.
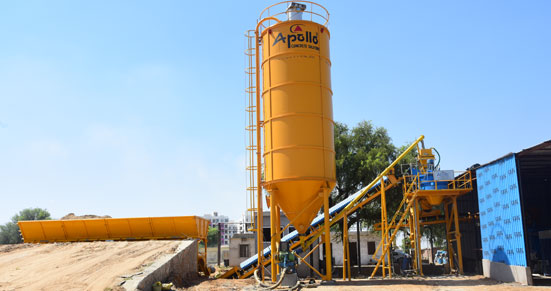
Available Models : ATP 90/100/120 – Engineered for High-Demand Projects
The ATP 90, 100 and 120 are the heavyweights of Apollo’s inline cement mixing plant range. Built to operate under the rigors of large-scale construction, these units are engineered for peak performance, continuous duty cycles and concrete consistency across multiple formulations.
What Sets These Models Apart?
- High Capacity Mixers: Capable of producing between 90 to 120 m³/hour, these plants meet the volume needs of the most demanding infrastructure builds.
- Flexible Concrete Recipes: Whether it’s high-strength concrete for bridges or flowable mixes for foundations, the batching systems accommodate multiple concrete types with minimal changeover time.
- Robust Design for Continuous Operation: With industrial-grade components and minimal moving parts, these plants are designed to run 24/7 with limited downtime.
- Dust and Moisture Control: Integrated systems ensure materials remain in optimal condition, improving batch quality and reducing waste.
When operating at such scales, even a few minutes of downtime can set back an entire project schedule. Hence, the ATP 90/100/120 models include proactive diagnostic tools and alerts, keeping your plant – and your timeline – on track.
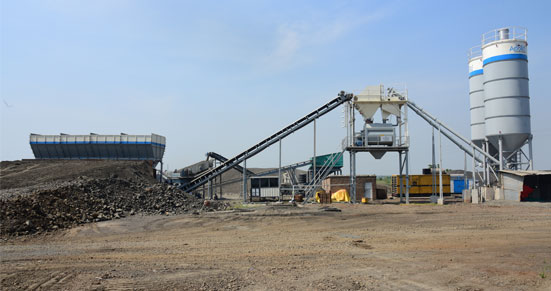
Maximizing Construction Timelines with Minimal Maintenance
One of the biggest times drains in traditional batching setups is the frequency of maintenance. Mechanical breakdowns, inconsistent outputs and manual calibration all slow production. Inline batching plants, particularly automated solutions, are engineered to minimize these interruptions.
How Inline Plants Streamline Maintenance:
- Pre-calibrated Load Cells: These helps maintain accurate batching for longer durations without manual recalibration.
- Self-cleaning Mixing Units: Reduce manual labor and downtime associated with cleaning hardened concrete.
- Digital Dashboards: Operators can monitor material levels, moisture content and mixing times in real-time, preventing errors before they escalate.
- Spare Part Accessibility: ATP plants are designed with modular components, ensuring quick swaps and easy part availability.
These features combine to give construction managers tighter control over the timeline, allowing for quicker project turnarounds and better resource planning.
On-Site Benefits: Operational Flexibility and Scalability
One of the standout advantages of inline plants is their ease of integration on construction sites. While traditional batching solutions may require significant civil work and logistics planning, inline type batching plants offer a plug-and-play setup.
Operational Benefits:
- Quick installation and dismantling: Perfect for project-based setups.
- Customizable configurations: Expand or reduce capacity as needed.
- Remote access control: Enables off-site monitoring and operational control.
- Energy-efficient components: Lower operational costs over time.
For engineering firms handling multiple projects simultaneously, this flexibility offers a serious advantage. Plants can be deployed across projects or scaled based on load requirements without major infrastructure changes.
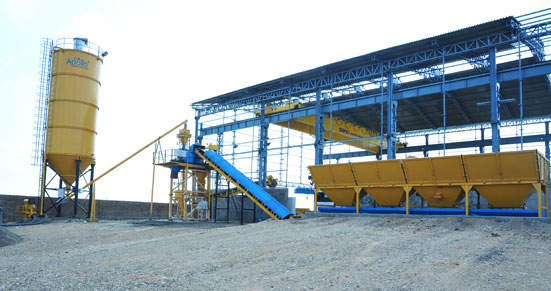
Inline Plant Safety and Environmental Adaptability
Safety and environmental controls are key concerns in any industrial operation. Apollo’s ATP models address these concerns with features designed to ensure operational safety and material handling cleanliness.
Safety & Environmental Features Include:
- Enclosed aggregate bins to reduce dust emission.
- Water recycling systems to minimize usage and discharge.
- Automatic alerts for overloading, overmixing or malfunctions.
- Guard rails and emergency stop mechanisms for on-site safety.
These features ensure compliance with local safety norms and reduce environmental impact – while also making daily operations smoother and safer for personnel.
Client Speaks
“Nice well organised management company.”
Conclusion
In today’s fast-paced construction world, time and quality are everything. The inline batching plant meets both requirements head-on, especially in large-scale infrastructure projects where there’s no margin for error. From Apollo’s ATP 90 to 120 models, the emphasis on high output, reduced maintenance, automation and mix versatility make these systems indispensable for engineers and construction managers alike.
Whether you’re building urban expressways, airport runways or industrial townships, integrating an inline concrete plant into your workflow can significantly cut down project timelines while ensuring product consistency. As infrastructure demands grow globally, the inline cement mixing plant stands out as a robust and reliable partner in building the future.
Table of Contents