Table of Contents
Introduction
Choosing the right concrete batching plant is crucial for the success of your construction project. With the right plant, you can ensure consistent quality, efficient production, and cost-effectiveness. This comprehensive guide will help you navigate the process of selecting the best batching plant based on your project requirements and budget. Let’s get started!
Understanding Your Project Requirements
The first step in choosing the right concrete batching plant is understanding the specific needs of your project.
Project Size and Scale
Consider the size and scope of your project. Large-scale infrastructure projects will require a high-capacity plant, while smaller residential projects might be adequately served by a smaller unit.
Types of Projects
- Commercial Projects: Office buildings, malls, and industrial facilities typically require high-quality concrete and consistent supply.
- Residential Projects: Homes, apartments, and condominiums might have different requirements, such as lower volume but more frequent batching.
- Infrastructure Projects: Roads, bridges, and dams need large quantities of durable concrete, often over extended periods.
Types of Concrete Batching Plants
Different types of batching plants are designed to meet varying project needs.
Stationary Batching Plants
- Features and Advantages: High production capacity, durable, ideal for long-term projects.
- Suitable Projects: Large-scale commercial and infrastructure projects.
Mobile Batching Plants
- Features and Advantages: Portability, flexibility, quick setup.
- Suitable Projects: Projects requiring frequent relocation, remote sites.
Dry Mix Plants
- Features and Advantages: Mixes dry ingredients, water added on-site, simple operation.
- Suitable Projects: Short transport distances, smaller projects.
Wet Mix Plants
- Features and Advantages: Pre-mixes all ingredients, ready-to-use concrete, high consistency.
- Suitable Projects: Immediate use projects, high-quality concrete needs.
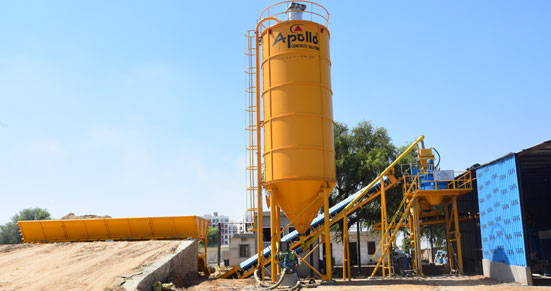
Key Factors to Consider
Production Capacity
Determine the required output for your project. Calculate the volume of concrete needed and ensure the plant’s capacity matches this requirement. A mismatch can lead to delays and inefficiencies.
Location and Mobility
Assess the project site. Is it a single location or spread across multiple sites? For single, large projects, a stationary plant is ideal. For projects requiring movement between sites, a mobile plant offers the best solution.
Budget Constraints
Consider both the initial investment and the ongoing operational and maintenance costs. Sometimes, a higher upfront cost can be justified by lower long-term expenses and better efficiency.
Technical Specifications
Mixing Efficiency
Consistency in mixing is critical for concrete quality. Different mixers offer varying levels of efficiency:
- Twin-shaft Mixers: High mixing intensity and short mixing times.
- Drum Mixers: Suitable for larger volumes.
- Pan Mixers: Ideal for smaller batches and specialty concrete.
Control Systems
Advanced control systems can automate the batching process, ensuring precision and reducing human error. Evaluate whether your project benefits from automation or if manual controls suffice.
Material Handling Systems
Efficient material handling ensures a smooth production process. Consider the types of conveyors, hoppers, and storage systems in the plant. Ensure they are capable of handling your specific materials efficiently.
Environmental Considerations
Modern concrete batching plants are designed with environmental concerns in mind. Look for plants with effective emission controls and dust management systems. Eco-friendly technologies can reduce the environmental impact and ensure compliance with regulations.
Quality Assurance and Certification
Ensure the batching plant is certified and complies with industry standards. Certified equipment guarantees reliability and quality, which is essential for the success of your project.
Supplier Reputation and Support
Choosing a reputable supplier can save you a lot of trouble down the road. Look for manufacturers with a strong track record, good customer reviews, and reliable after-sales support. The availability of spare parts and prompt service can significantly impact your plant’s uptime and efficiency.
Conclusion
Choosing the best concrete batching plant involves considering multiple factors, including project requirements, plant types, production capacity, budget, technical specifications, environmental impact, quality assurance, and supplier reputation. By carefully evaluating these aspects, you can select a plant that ensures efficiency, quality, and cost-effectiveness for your project.
Table of Contents