Table of Contents
Mobile concrete batching plants have become an essential asset for construction projects requiring on-site, consistent, and high-quality concrete. Selecting the right design and capacity is critical for ensuring efficiency and productivity. This guide covers the essential design considerations-mobility, setup time, durability, and maintenance-and provides insight into selecting the ideal capacity based on project size, usage frequency, and volume requirements.
Key Design Considerations for Mobile Concrete Batching Plants
When choosing a mobile concrete batching plant, understanding design factors that impact performance, cost, and usability is crucial.
1. Mobility
- Importance of Portability: Mobility is one of the main benefits of mobile batching plants, designed to be easily transported between sites. This makes them ideal for projects spread across multiple locations or sites where permanent infrastructure is impractical.
- Design Aspects to Consider: Look for units that have compact designs and are mounted on wheels or trailers. Additionally, ensure the plant is compliant with local transport regulations regarding dimensions and weight.
2. Setup Time
- Efficiency in Installation: One of the major advantages of mobile plants is rapid setup time. Unlike stationary plants, which require extensive groundwork, mobile units are designed for a quick assembly process.
- Key Design Features: Some plants feature a “plug-and-play” design, allowing them to be operational within hours. Ensure the model chosen has straightforward installation steps and doesn’t require a large crew for setup. Quick setup times lead to faster productivity, which is especially important for time-sensitive projects.
3. Durability
- Robust Construction for Long-Term Use: Mobile concrete batching plants often face tough conditions. From frequent moves to varied weather, the plant’s durability is key for longevity and low maintenance costs.
- Material and Build Quality: Choose a model built with high-quality, weather-resistant materials such as stainless steel or coated metal that resists corrosion. Heavy-duty chassis, reinforced frame, and rugged components will also extend the plant’s life and improve performance under demanding conditions.
4. Ease of Maintenance
- Regular Maintenance for Consistent Output: Ease of maintenance impacts not only the plant’s longevity but also the consistency and quality of the concrete it produces.
- Design Considerations for Maintenance: Opt for models that have easy access to wear parts, filters, and mixer drums. Automated cleaning systems can also reduce downtime and improve overall efficiency. Routine maintenance checks are easier with user-friendly control panels and diagnostic tools integrated into modern mobile batching plants.
Choosing the Right Capacity for Mobile Concrete Batching Plants
Capacity is one of the most critical factors to consider when selecting a mobile concrete batching plant. The right capacity will depend on the project requirements, expected frequency of use, and the concrete volume required.
1. Project Size and Scope
- Large-Scale Projects: High-capacity plants are better suited for large-scale projects that require large volumes of concrete in a short time. Typically, high-capacity plants can produce upwards of 100 cubic meters of concrete per hour, making them ideal for major infrastructure projects.
- Small to Medium Projects: For smaller projects, a medium or low-capacity plant might be more efficient and cost-effective. Mobile plants with a capacity of 20–50 cubic meters per hour can cater to medium-sized projects or those with modest daily concrete needs.
2. Frequency of Use
- Frequent Use Requirements: Projects with ongoing and frequent concrete needs will benefit from a higher-capacity plant with robust design features that withstand constant use. Look for plants with automated control systems and high-quality mixing components to ensure consistent concrete quality over time.
- Occasional or Intermittent Use: For projects with intermittent requirements, such as small development projects or temporary setups, a lower-capacity plant that’s easy to move and set up quickly is preferable.
3. Concrete Volume Requirements
- Daily Volume Output Needs: Calculate the required concrete volume for daily output to determine the plant’s ideal capacity. Most batching plants measure capacity in cubic meters per hour, so you’ll want to match the plant’s output capability with your project’s needs.
- Avoiding Overcapacity or Undercapacity: Choosing the right capacity helps avoid the inefficiencies and costs associated with overcapacity or undercapacity. If the plant’s capacity is too low, production delays could occur, whereas a plant with excessive capacity can lead to unnecessary operational costs and underutilized equipment.
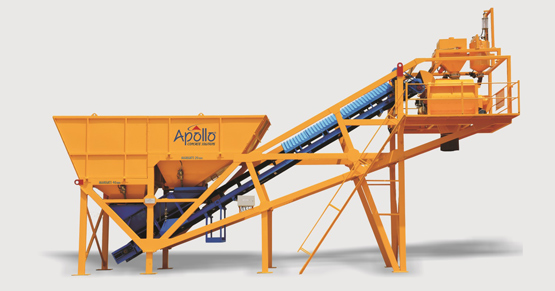
Final Thoughts: Making the Right Purchase Decision
Investing in a mobile concrete batching plant requires careful consideration of both design and capacity. By focusing on key design elements such as mobility, setup time, durability, and maintenance, you can ensure that the plant will be resilient and reliable. Likewise, selecting a capacity that aligns with project demands ensures both efficiency and cost-effectiveness.
Whether your needs involve a high-capacity plant for large-scale construction or a compact, easy-to-move model for smaller sites, balancing these factors will enable you to choose the best plant for consistent, high-quality concrete production.
Table of Contents