Table of Contents
Introduction
Operating a concrete block making machine correctly is crucial for ensuring safety, efficiency, and the production of high-quality blocks. This step-by-step guide provides detailed instructions on how to operate a concrete block making machine safely and efficiently, helping you achieve the best results for your project. Investing in high-quality concrete block making equipment ensures durability and precision in block production, minimizing errors and enhancing efficiency.
Preparing for Operation
Safety Measures and PPE
Before starting the machine, ensure that all safety measures are in place. Operators should wear appropriate personal protective equipment (PPE) such as safety glasses, gloves, and ear protection. Make sure that all safety guards are in position and functioning correctly.
Inspecting the Machine
Conduct a thorough inspection of the machine to ensure all parts are in good working condition. Check for any signs of wear, damage, or loose components. Ensure that all moving parts are properly lubricated. Proper maintenance and regular inspections of concrete block making equipment help extend its lifespan and reduce the risk of breakdowns during production.
Preparing the Work Area
Ensure the work area is clean and free of any obstructions. Set up barriers or warning signs to keep unauthorized personnel away from the machine during operation.
Understanding the Machine Components
Familiarize yourself with the key components of the concrete block making machine:
- Hopper: Holds the raw materials.
- Mixer: Mixes the raw materials to form a homogeneous mixture.
- Mold: Shapes the concrete mix into blocks.
- Control Panel: Manages the operation of the machine.
- Conveyor: Transports the blocks to the curing area.
Understanding the functions of each component is essential for efficient operation.
Initial Setup and Calibration
Setting Up the Machine
Position the machine on a flat, stable surface. Ensure that it is securely anchored to prevent movement during operation. Connect the machine to the power supply and check that all connections are secure.
Calibrating Molds and Settings
Calibrate the molds to ensure they are correctly aligned and set to the desired block size. Adjust the settings on the control panel to match the specifications of your project, including the mix ratio and compaction pressure.
Using advanced concrete block making equipment allows for precise calibration, ensuring uniform block size and high structural integrity.
Loading Raw Materials
Types of Raw Materials
The primary raw materials for concrete blocks include cement, sand, gravel, and water. Depending on the block type, you might also need additives for strength or color.
Correct Proportions and Mixing
Measure the raw materials accurately according to the mix design. Use the mixer to combine the materials until a uniform consistency is achieved.
Loading Materials into the Machine
Load the mixed materials into the hopper of the block making machine. Ensure the hopper is not overloaded to avoid spillage and ensure smooth operation.
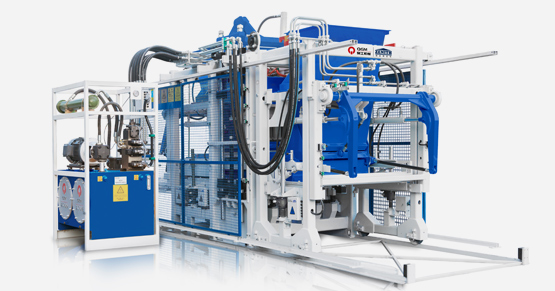
Starting the Machine
Turning on the Power
Switch on the power to the machine and allow it to initialize. Check the control panel to ensure all systems are functioning correctly.
Operating the Control Panel
Use the control panel to start the production process. Follow the manufacturer’s instructions to set the machine to the correct mode and initiate the block making cycle.
Initial Trial Run
Conduct an initial trial run to ensure that the machine is operating correctly. Produce a few test blocks to check for consistency and quality. Modern concrete block making equipment enhances automation, reducing manual intervention and improving overall production efficiency.
Production Process
Feeding the Mix into the Mold
The machine will automatically feed the mix into the mold. Ensure the mold is filled evenly to avoid defects in the blocks.
Compacting the Mix
The machine will compact the mix in the mold to form solid blocks. Ensure the compaction pressure is set correctly to achieve the desired block density.
Curing and Drying Blocks
After forming, the blocks need to be cured to achieve their full strength. Transport the blocks to a curing area and follow the recommended curing process.
Removing and Stacking Blocks
Once cured, remove the blocks from the molds and stack them carefully to avoid damage. Store the blocks in a dry, sheltered area until ready for use.
Monitoring and Adjustments
Continuous Monitoring During Operation
Monitor the machine continuously during operation to ensure it is running smoothly. Check for any irregularities in block quality or machine performance.
Making Necessary Adjustments
If any issues arise, make the necessary adjustments to the machine settings. This could include adjusting the mix ratio, compaction pressure, or mold alignment.
Ensuring Consistency in Block Quality
Regularly check the blocks for consistency in size, shape, and strength. Adjust the production process as needed to maintain high-quality standards.
Troubleshooting Common Issues
Identifying Common Problems
Common issues include block defects, machine jams, and inconsistent block quality. Identify these problems early to minimize downtime.
Steps to Resolve Issues
Follow the manufacturer’s troubleshooting guide to resolve common issues. This might involve adjusting settings, cleaning components, or replacing worn parts.
When to Call for Professional Help
If the machine experiences a significant malfunction or if you are unable to resolve an issue, contact a professional technician for assistance.
Shutting Down the Machine
Proper Shutdown Procedures
Turn off the power to the machine and follow the manufacturer’s shutdown procedures. This ensures the machine is safely powered down and ready for the next use.
Cleaning the Machine
Clean the machine thoroughly after each use. Remove any residual mix from the hopper, molds, and conveyor to prevent buildup and ensure smooth operation.
Performing Maintenance Checks
Conduct routine maintenance checks after each use. This includes inspecting components for wear and tear, lubricating moving parts, and checking the electrical system.
Maintenance Tips
Regular Maintenance Routines
Establish a regular maintenance schedule to keep the machine in top condition. This includes daily, weekly, and monthly maintenance tasks.
Lubrication and Parts Replacement
Ensure all moving parts are properly lubricated to reduce friction and wear. Replace worn or damaged parts promptly to prevent further issues.
Keeping a Maintenance Log
Maintain a detailed log of all maintenance activities. This helps track the machine’s condition and identify any recurring issues.
Training and Best Practices
Training Staff to Operate the Machine
Provide thorough training for all operators. Ensure they understand how to operate the machine safely and efficiently.
Best Practices for Efficient Operation
Implement best practices such as regular monitoring, timely maintenance, and adherence to safety protocols to ensure efficient operation.
Safety Protocols and Emergency Procedures
Establish clear safety protocols and emergency procedures. Ensure all staff are familiar with these protocols and know how to respond in case of an emergency.
Conclusion
Operating a concrete block making machine correctly involves understanding the machine components, following proper setup and operation procedures, and maintaining the machine regularly. By adhering to these guidelines, you can ensure safe, efficient operation and produce high-quality blocks for your projects.
Table of Contents