Table of Contents
Mobile Concrete Batching Plants and Inline Concrete Batching Plants are two distinct types of setups used in the production of concrete, each with its own advantages and specific use cases. Below, we explore the differences, benefits, and limitations of each system to help potential users and industry professionals make informed decisions based on their specific needs.
Mobile Concrete Batching Plants
1. Mobility and Flexibility
Mobile concrete batching plants are designed for temporary installation and easy relocation. They are ideal for projects that require the batching plant to be moved between sites, such as road construction and remote area applications. The mobility feature offers high flexibility, especially when dealing with multiple construction sites or projects with short timelines.
2. Installation and Setup
These plants are pre-wired and pre-assembled, which greatly reduces the setup and dismantling time. Typically, they can be transported on trailers and do not require extensive site preparation or foundations, which can be costly and time-consuming.
3. Cost-Effectiveness
Mobile batching plants are generally more cost-effective for short-term projects or projects at multiple sites because they reduce transportation costs of the concrete from a static plant location to various construction sites.
4. Production Capacity
While mobile concrete batching plants are highly efficient, their production capacity is usually lower than that of stationary inline plants. They are designed to produce batches of concrete, sufficient for smaller-scale projects or where the demand for concrete varies.
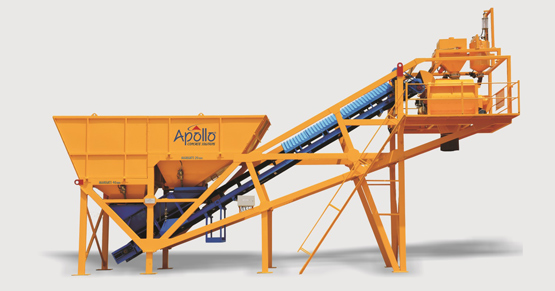
5. Operational Limitations
The compact nature of mobile plants often means they have fewer storage bins for aggregate and limited space for other raw materials. This can impact the range of concrete types they can produce without restocking.
Inline Concrete Batching Plants
1. Higher Production Capacity
Inline concrete batching plants are stationary and designed for permanent setups, making them suitable for large-scale industrial projects and commercial concrete production. Their production capacity is typically much higher than that of mobile plants, allowing them to meet the demands of sustained, high-volume concrete output.
2. Complex Installation
Unlike mobile plants, inline batching plants require significant site preparation, including the construction of solid foundations and infrastructure. This preparation leads to longer setup times and potentially higher initial capital investments.
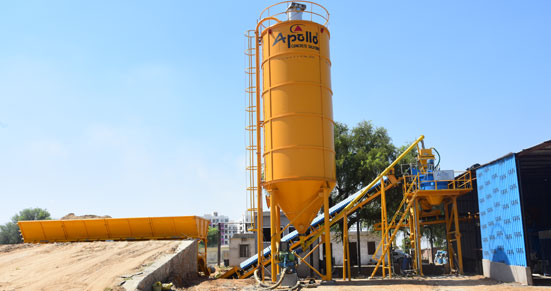
3. Enhanced Material Storage
These plants are usually larger and have extensive material storage capacity. This allows for a greater variety of concrete mixes to be produced efficiently and reduces the frequency of restocking required. They can accommodate larger silos for cement, multiple aggregate bins, and enhanced facilities for admixtures and other components.
4. Durability and Longevity
Being designed for permanent installation, inline batching plants are built to be more robust and durable. They are capable of operating continuously over longer periods, making them ideal for projects with a prolonged duration.
5. Reduced Flexibility
The major limitation of inline plants is their lack of mobility. Once established, these plants are not easily moved, which can be a drawback for companies that work on projects in various locations.
Conclusion
The choice between a mobile concrete batching plant and an inline concrete batching plant depends largely on the project requirements, duration, and location. Mobile plants offer greater flexibility and cost-efficiency for dynamic projects involving multiple locations or temporary sites. In contrast, inline plants are better suited for long-term projects with high volume demands, where the initial higher investment can be justified over time through efficient, large-scale production. Understanding these key differences can guide users in choosing the most appropriate batching plant type to maximize productivity and operational efficiency.
Table of Contents